Maximizing Equipment Efficiency Through Packaging Machine Repair
Maximizing Equipment Efficiency Through Packaging Machine Repair
Blog Article
Quick and Reliable Product Packaging Maker Repair Service Services to Minimize Downtime
In the affordable landscape of manufacturing, the efficiency of product packaging operations rests on the integrity of equipment. Quick and dependable repair solutions are important in mitigating downtime, which can bring about considerable financial losses and functional problems. Recognizing the relevance of timely treatments and the function of expert professionals can transform just how companies come close to maintenance and fixings. Nevertheless, browsing the myriad options readily available for repair work solutions can be difficult. What elements should organizations consider to guarantee they are making the appropriate choice for their functional demands?
Relevance of Timely Repairs
Timely repairs of packaging machines are essential for preserving operational efficiency and reducing downtime. In the fast-paced environment of production and packaging, also small breakdowns can result in significant delays and productivity losses. Addressing issues promptly makes certain that equipments run at their optimum capability, thus protecting the flow of operations.
In addition, normal and prompt upkeep can stop the acceleration of minor problems right into major failures, which often sustain greater repair work costs and longer downtimes. An aggressive technique to device repair not just protects the integrity of the tools however additionally improves the total reliability of the assembly line.
In addition, prompt repair work add to the durability of packaging equipment. Devices that are serviced promptly are much less likely to endure from extreme wear and tear, enabling businesses to optimize their investments. This is specifically essential in sectors where high-speed packaging is essential, as the requirement for regular performance is paramount.
Benefits of Reliable Provider
Reputable solution providers play a pivotal role in guaranteeing the smooth operation of packaging makers. Their experience not just boosts the efficiency of repairs but also contributes significantly to the longevity of equipment.

In addition, a trusted provider uses detailed assistance, including training and advice for staff on maker operation and upkeep best practices. This not just encourages staff members but additionally cultivates a society of security and performance within the organization. Generally, the advantages of involving trusted company expand past instant fixings, favorably affecting the whole functional workflow of product packaging processes.
Common Product Packaging Device Concerns
In the realm of packaging operations, numerous issues can jeopardize the effectiveness and capability of machines (packaging machine repair). Another typical concern is misalignment, which can cause jams and uneven packaging, affecting product quality and throughput.
Electric issues can likewise interrupt product packaging procedures. Damaged wiring or malfunctioning sensors may cause erratic maker habits, creating hold-ups and boosted functional costs. Additionally, software application problems can prevent the machine's programming, causing functional ineffectiveness.
Irregular product flow is one more essential issue. This can arise from variants in item size, weight, or form, which might influence the maker's capability to manage things precisely. Inadequate training of drivers you can try here can aggravate these troubles, as inexperienced personnel might not acknowledge early signs of breakdown or may abuse the devices.
Resolving these typical product packaging maker concerns promptly is crucial to keeping performance and making sure a smooth operation. Normal evaluations and positive maintenance can significantly alleviate these concerns, cultivating a reputable product packaging setting.
Tips for Decreasing Downtime
To minimize downtime in product packaging operations, carrying out an aggressive upkeep method is vital. Frequently arranged upkeep checks can recommended you read identify possible problems before they intensify, guaranteeing devices operate efficiently. Developing a routine that includes lubrication, calibration, and assessment of essential parts can dramatically lower the regularity of unforeseen break downs.
Training staff to run equipment appropriately and recognize very early caution signs of malfunction can additionally play a crucial function. Empowering operators with the understanding to carry out basic troubleshooting can protect against small issues from causing significant hold-ups. Maintaining a well-organized stock of necessary spare parts can quicken repair work, as waiting for components can lead to extensive downtime.
Furthermore, recording device efficiency and upkeep activities can assist recognize patterns and persistent problems, permitting targeted treatments. Including advanced tracking technologies can offer real-time information, making it possible for anticipating maintenance and minimizing the risk of unexpected failings.
Last but not least, fostering open communication between operators and maintenance teams guarantees that any type of irregularities are promptly reported and resolved. By taking these positive steps, services can boost functional efficiency and considerably reduce downtime in packaging processes.
Picking the Right Repair Solution
Choosing the appropriate repair work service for product packaging makers is a crucial choice that can substantially impact functional efficiency. Begin by reviewing the company's experience with your certain type of product packaging equipment.
Following, consider the provider's online reputation. Seeking feedback from various other organizations within your market can give insights into reliability and high quality. Accreditations and partnerships with identified equipment suppliers can also suggest a dedication to excellence.
In addition, evaluate their feedback time and availability. A provider who can use punctual support lessens downtime and maintains production flow consistent. It's additionally essential to make inquiries concerning warranty and service assurances, which can mirror the confidence the company has in their job.
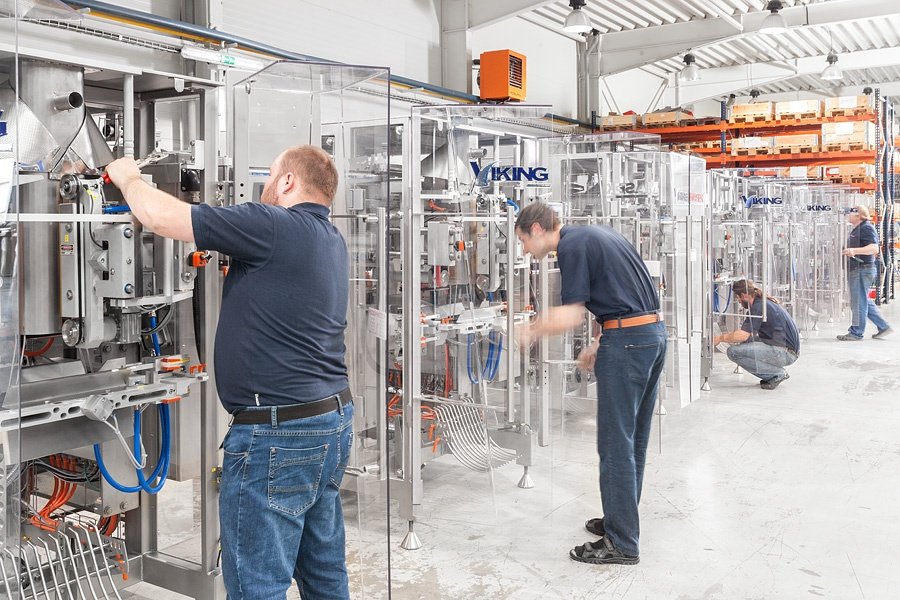
Verdict
In verdict, the significance of quick and trustworthy product packaging equipment repair services can not be overemphasized, as they play a critical role in reducing downtime and making sure functional efficiency. Executing positive upkeep techniques and spending in team training further enhances the longevity of packaging machinery.
Prompt repair services of product packaging equipments are crucial for maintaining operational effectiveness and reducing downtime.Furthermore, timely repair services add to the durability of product packaging equipment. Generally, the benefits of involving reliable service providers extend past prompt fixings, favorably influencing the whole functional process of packaging processes.
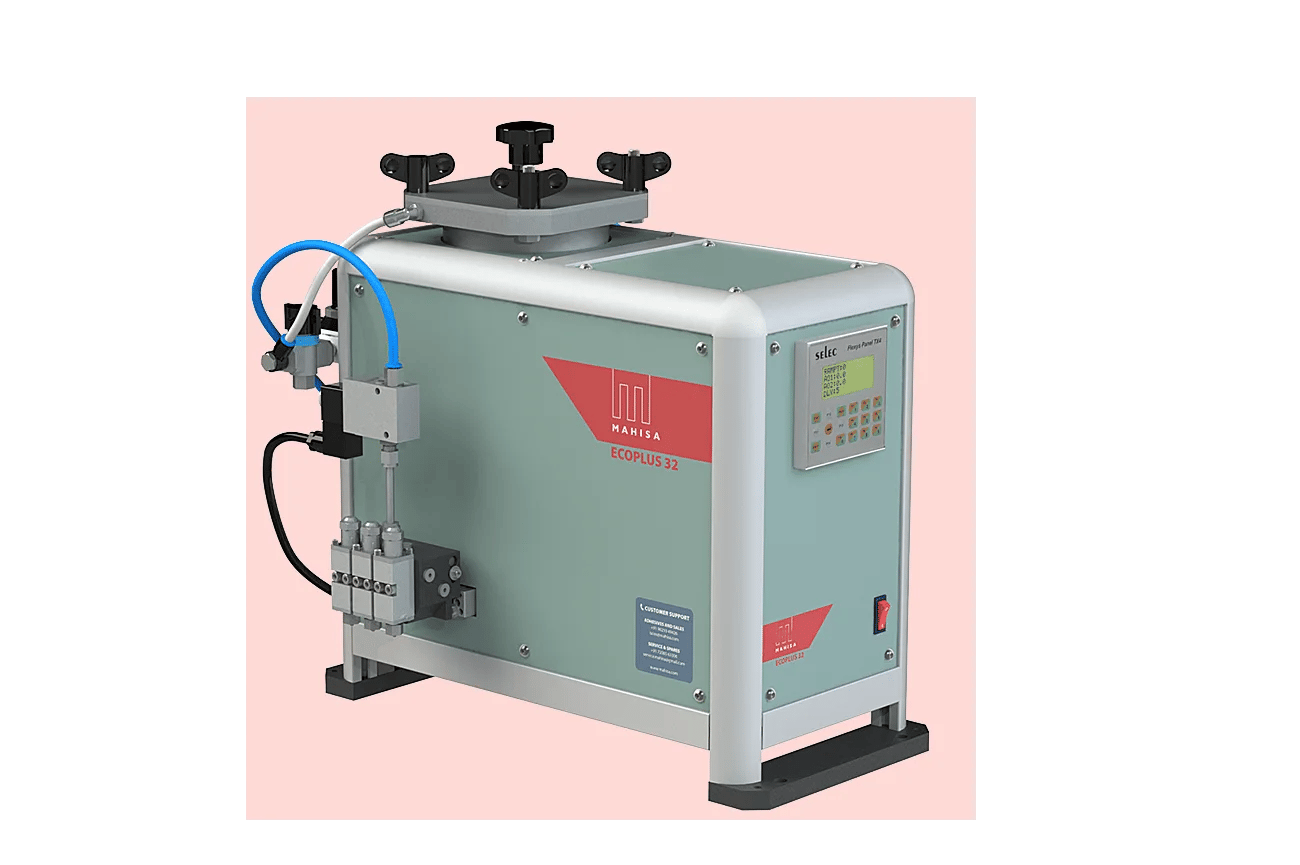
Report this page